- Out-of-Stock
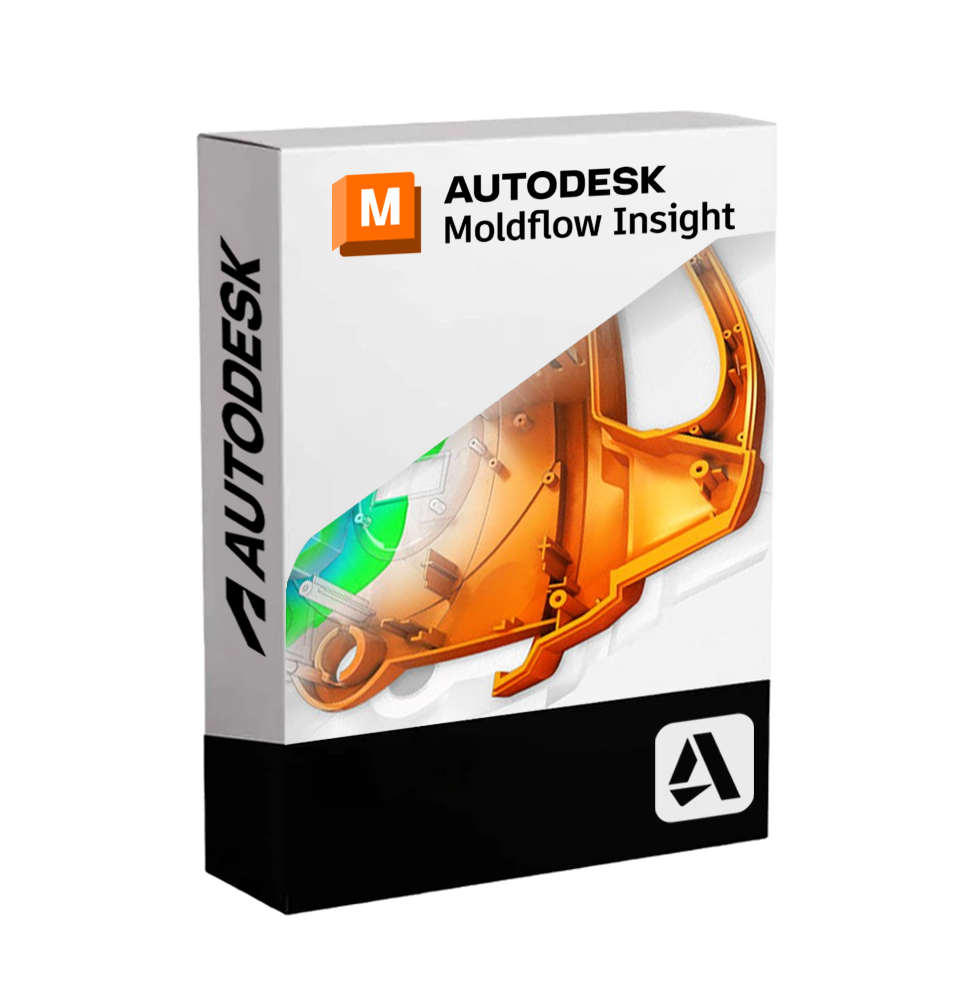
DISCOUNT -10% - use the code SAT10 valid without minimum order
Autodesk Moldflow Insight – Advanced Simulation of Injection Molding for Plastic Process Optimization
Autodesk Moldflow Insight is the reference software for advanced analysis of plastic injection molding processes. Designed for engineers, technicians, and mold designers, this tool allows for extremely accurate simulation and optimization of the production of plastic components, reducing time and costs associated with physical testing and increasing the reliability of the final product.
Moldflow Insight allows you to anticipate defects, optimize mold design, and validate the behavior of materials during processing, improving the overall efficiency of industrial production.
Main Features of Autodesk Moldflow Insight
•Complete simulation of the molding process: including filling, compression, cooling, compaction, deformation, and shrinkage of the piece.
•Support for thermoplastic, thermosetting, and composite materials: with a vast database of updated industrial materials, validated by certified suppliers.
•Analysis of molding defects: prediction of common problems such as air traps, weld lines, warpage, sink marks, and unfilled cavities, with interactive visualization tools 🔍.
•Optimization of the feeding system: evaluation of the optimal position of injection channels, sizing of nozzles, runners, and gates, and design of integrated cooling systems.
•Multi-cavity analysis and balancing: simulation of multi-impression molds to ensure balanced and consistent filling in each cavity.
•Evaluation of deformations (warpage): precise estimation of post-cooling distortions, with suggestions for geometric compensation.
•Advanced simulations: overmolding, molding with inserts, bi-material, co-injection, gas-assisted injection molding, powder injection molding.
•Integration with CAD and PLM: direct compatibility with files from Autodesk Inventor, Fusion 360, SolidWorks, CATIA, Siemens NX, PTC Creo, and other 3D CAD software ✨.
•Thermal and cooling analysis: complete modeling of cooling circuits, conductive materials, and heat dissipation within the mold.
Technologies included in the Insight version
Moldflow Insight offers specific tools for the most complex needs, including:
•Multiple solvers (Dual Domain, Midplane, 3D): for different levels of detail and computational performance
•Batch solving and remote management of simulations: useful for large teams or companies with distributed computing centers
•Parametric and automatic optimization analysis: to compare multiple design scenarios and find the best solution
•Integration with design of experiment (DOE) tools and Six Sigma methodologies for continuous quality improvement
Compatibility and System Requirements
Supported operating systems:
•Windows 10 / 11 (64-bit) - Linux
Moldflow Insight is not compatible with macOS
Recommended minimum requirements:
•Processor: Intel Core i7 or AMD Ryzen 7 (recommended processor with 8 or more cores)
•RAM: minimum 32 GB (recommended 64 GB or more for complex 3D simulations)
•Graphics Card: NVIDIA Quadro or equivalent, OpenGL-compatible, at least 4 GB VRAM
•Disk space: at least 50 GB free for installation and temporary files
•Internet Connection: necessary for activation and software updates ☁️
Who is Autodesk Moldflow Insight suitable for?
Moldflow Insight is the ideal tool for:
•Plastic engineers and mold technicians who need to ensure the quality and efficiency of the molding process
•Mold manufacturers and workshops specialized in the design of injection molding equipment
•Companies in the automotive, medical, electronic, and packaging sectors that use critical plastic components 🏭
•Research and development laboratories that analyze new materials or develop innovative geometries
•Universities and training centers that teach advanced industrial production technologies
✅ Autodesk Moldflow Insight represents one of the most powerful solutions in the world for accurately simulating every phase of injection molding. It reduces the risk of errors, improves production efficiency, and allows for the design of pieces and molds with a solid and verifiable scientific basis. An indispensable ally for those working in the heart of the plastic industry.